Polymer Science: Driving Innovation in Health and Industry
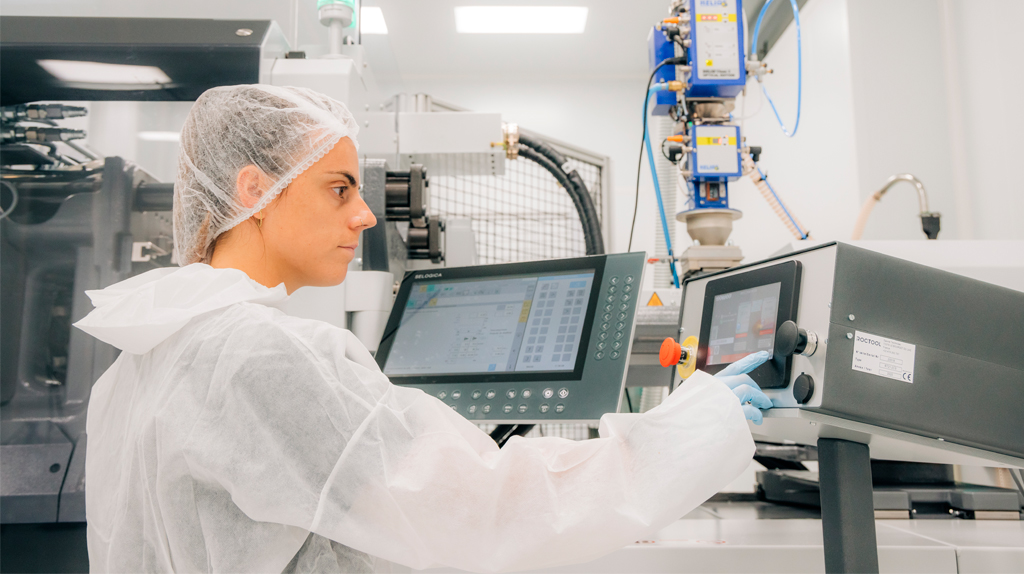
Polymer science enables the production of devices for a wide range of applications, including biomedical diagnostic (such as point-of-care diagnostics, personalized medicine, drug screening and organ-on-a-chip models), environmental monitoring (covering air and water quality) and industrial applications (like food and beverage quality control).
Natural and synthetic polymer offer advantages including flexibility, biocompatibility and structural integrity, which are essential parameters for maintaining functionality under mechanical and chemical stresses. Depending on application requirements, the physical and chemical properties of polymers—such as mechanical strength, chemical resistance, optical properties, and electrical conductivity—can be modified. This adaptability allows polymers to be tailored to be flexible or rigid, transparent or opaque, and conductive or insulating.
Injection molding: a common mass manufacturing technique for polymer devices.
In this process, molten polymer is injected into a mold cavity at high pressure. The injection molding process involves several steps:
- Heating of the polymer to a molten state.
- Injection the molten polymer into a precision-engineered mold.
- Cooling and solidifying the polymer.
- Opening the mold.
- Ejecting the finished part.
Moreover, this method enables the production of large quantities of devices with a consistent quality and structural integrity. It allows the production of complex geometries and high aspect ratios ideal for the commercialization of the products. The advantages of injection molding include high production rates, excellent repeatability, and the ability to produce intricate shapes with high precision.
Selecting the appropriate polymer is crucial for these applications, as the thermal and rheological properties must be suitable for the injection molding process.
Polydimethylsiloxane (PDMS) is widely used resin for prototyping, but it is not a compatible material for injection molding. Materials that are compatible with injection molding include poly(methyl methacrylate) (PMMA), cyclic olefin copolymers (COC) and polycarbonate (PC), among others. PMMA offers excellent optical properties and chemical resistance. COC and cyclic olefin polymers (COP) serve as alternatives for PDMS and PMMA, providing high chemical resistance and low water absorption. PC is a suitable material if the application requires a high mechanical strength and thermal resistance.
At this time, Erreka Medical specializes in manufacturing injection-molded polymer parts for medical devices. The most commonly used materials include PMMA, COC, COP, PC, and PS. For any inquiries about their processes, please feel free to contact us via email at medical@erreka.com or by filling out the form in the contact area of our website.
News
We tell you the latest news about ERREKA.
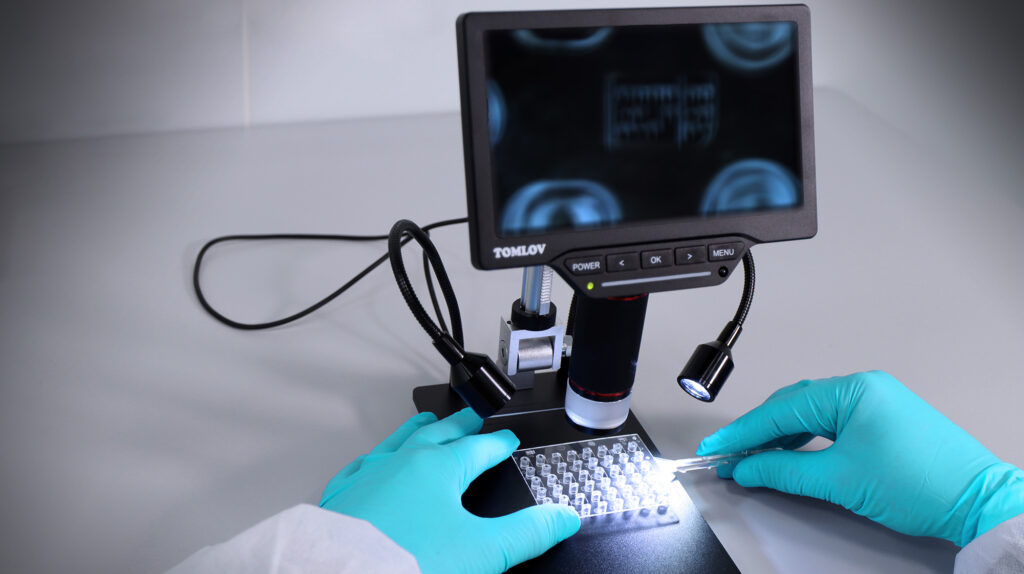
IVD Raw materials
With the enhancement of medical science and technology, there’s a growing need for real-time diagnostic devices. Many compact systems have […]
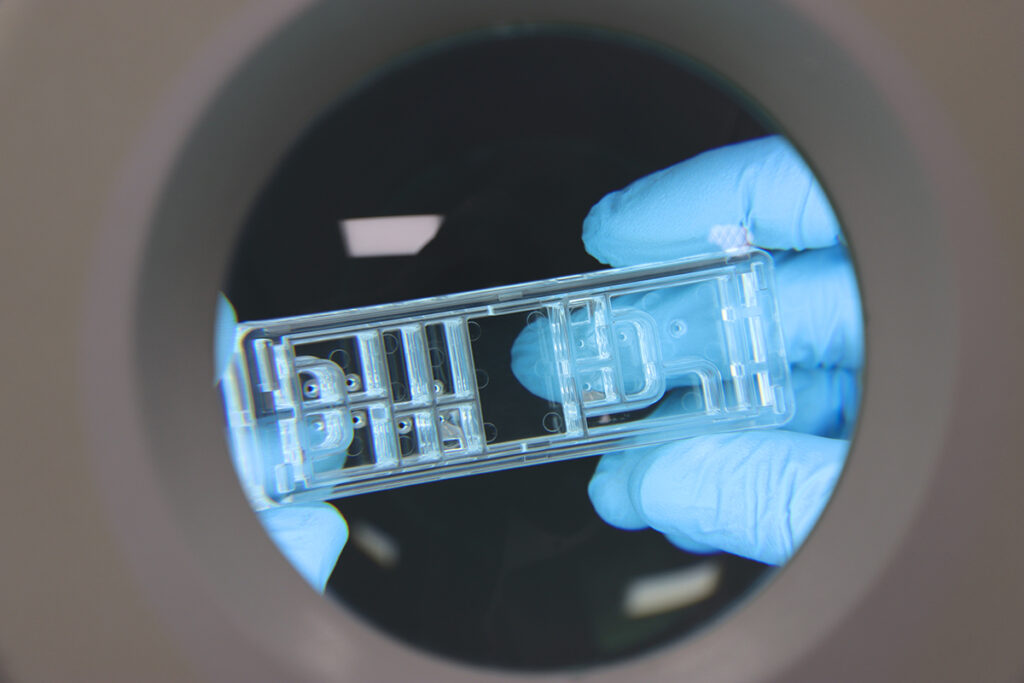
From glass chips to polymer chips: revolutionizing microfluidic technology
For many years, glass chips have been integral to biomedical applications, notably in microfluidic technology. However, recent advancements have illuminated […]
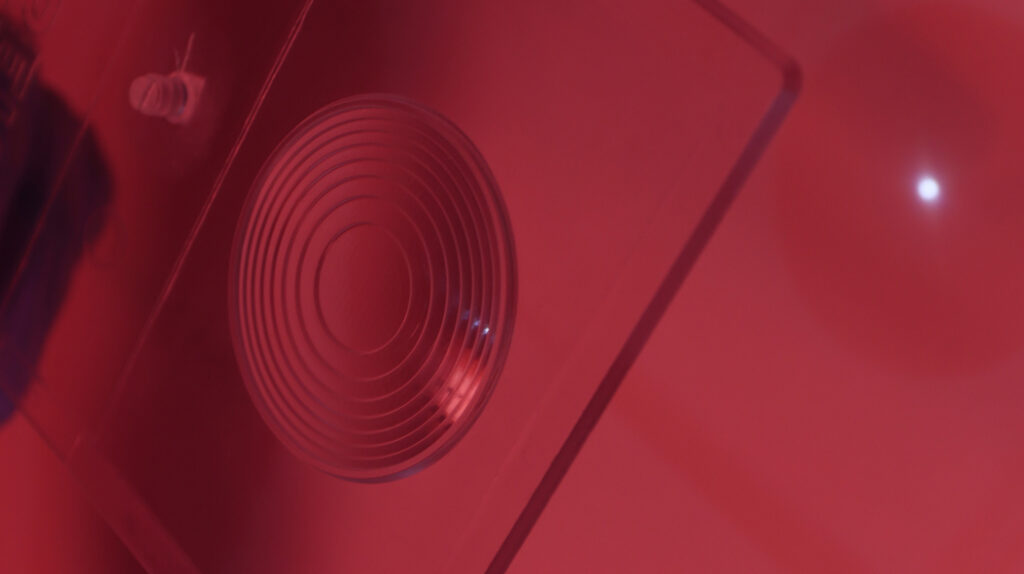
Injection molding microfluidics process definition
In applications involving low stress, thin walls, and microstructure replication, achieving the desired results heavily relies on precisely setting the […]