IVD Raw materials
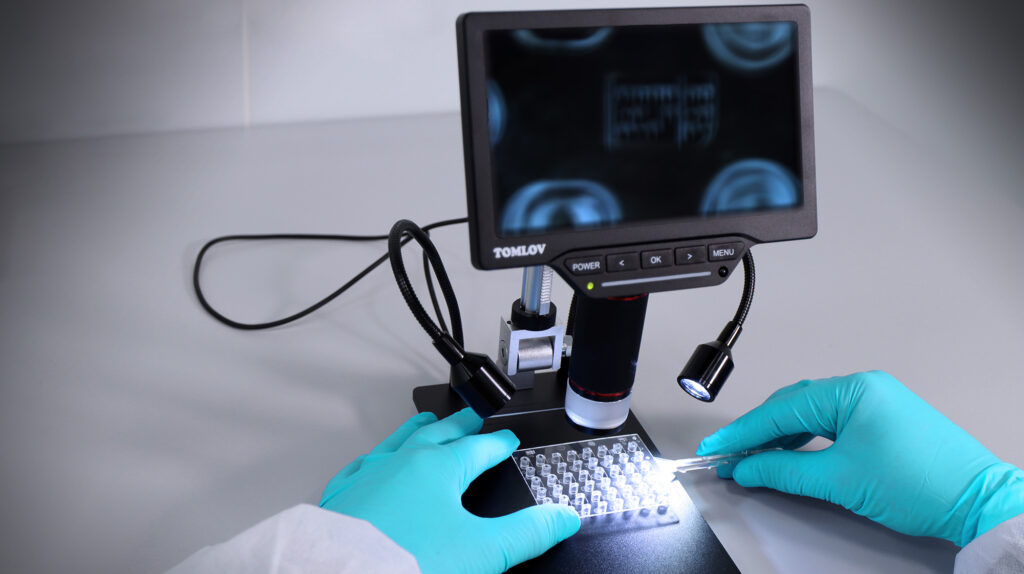
With the enhancement of medical science and technology, there’s a growing need for real-time diagnostic devices.
Many compact systems have been successful, covering a range of areas like DNA microarrays, chip-based polymerase chain reaction (PCR), peptide and oligonucleotide libraries, drug screening, cell culture, and the innovative concept of microsystems mimicking living systems, which could replace animal testing and make improvements towards personalized diagnostics, tailoring treatments to individual needs.
Recent advancements in in vitro diagnostic (IVD) tests, particularly the development of versatile and smaller lab-on-a-chip (LoC) microsystems, signify a growing trend in healthcare. IVD tests involve analyzing biological samples like blood, urine, tissue, or saliva outside of the living organism (in vitro) to diagnose various medical conditions, diseases, or infections. The integration of precise fluid handling, complex sample processing, signal detection, and readout functions in these systems facilitates easier disease monitoring, health assessment, and infection detection, thus enhancing disease management, treatment, and prevention strategies.
Thermoplastics are commonly chosen as raw materials for IVD applications due to their versatility, ease of processing, biocompatibility, chemical resistance, and optical transparency, among other properties. This transparency is crucial for optical detection methods in diagnostic assays, allowing for accurate analysis of biological samples.
The thermoplastics that are most commonly used in our injection molding machines and its properties are shown below:

These materials offer a unique combination of properties that make them ideal for a wide range of applications for IVD devices.
ERREKA: Your Trusted Partner for contract manufacturing of polymer components for medical devices.
Above that Erreka developed the knowledge to be a solid partner for the polymer components need in the medical device market. Several components have been injected in our ISO 8 clean room using different injection process types such as Standard injection molding, Injection –compresion molding, or Heat&Cool injection process and always following the ISO13485 standard.
Contact us if you have any need for microfluidic devices.
News
We tell you the latest news about ERREKA.
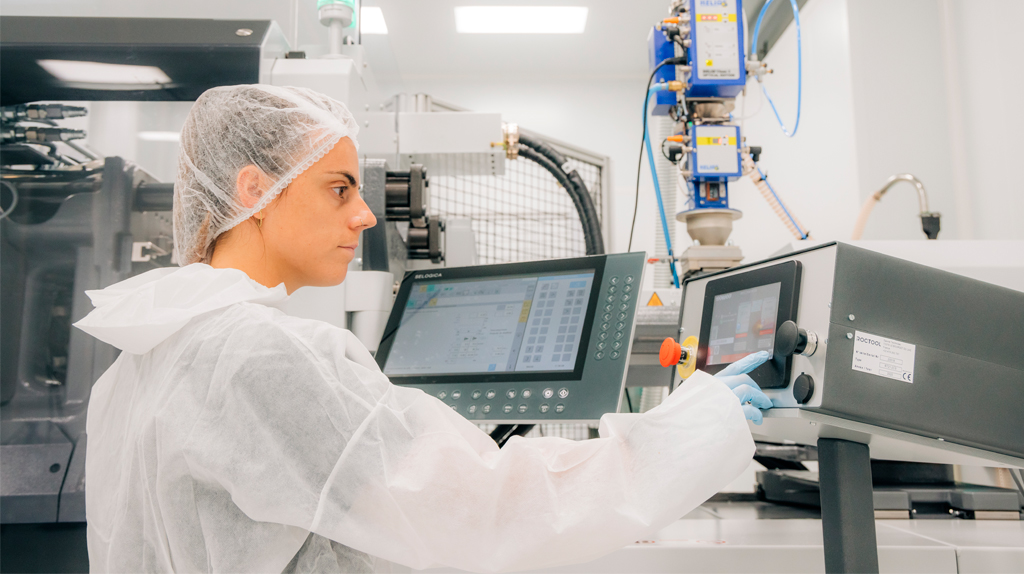
Polymer Science: Driving Innovation in Health and Industry
Polymer science enables the production of devices for a wide range of applications, including biomedical diagnostic (such as point-of-care diagnostics, […]
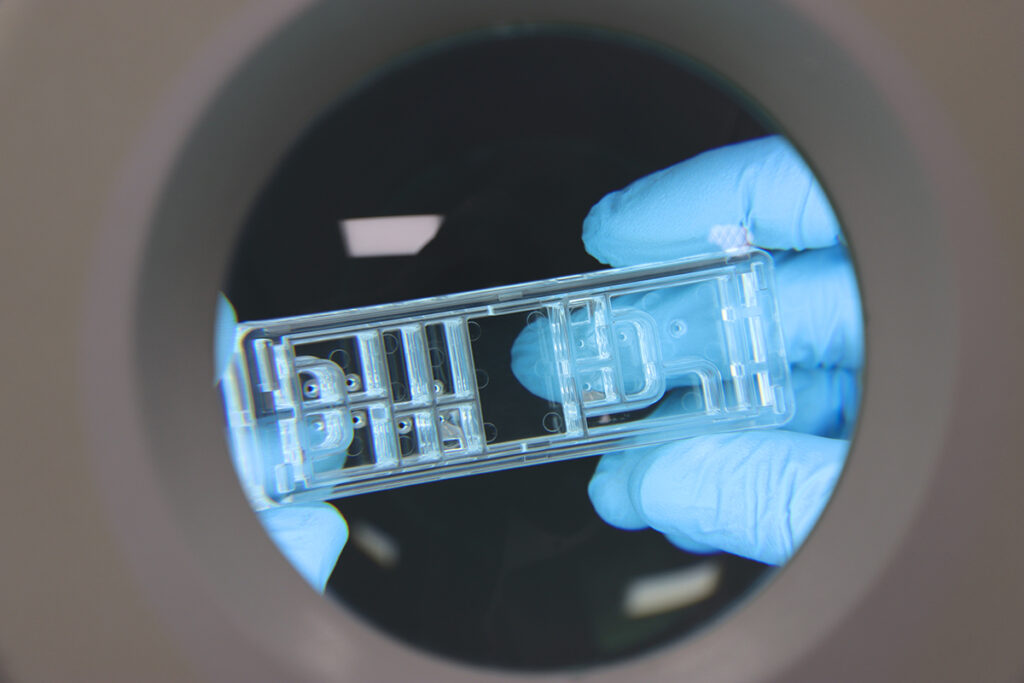
From glass chips to polymer chips: revolutionizing microfluidic technology
For many years, glass chips have been integral to biomedical applications, notably in microfluidic technology. However, recent advancements have illuminated […]
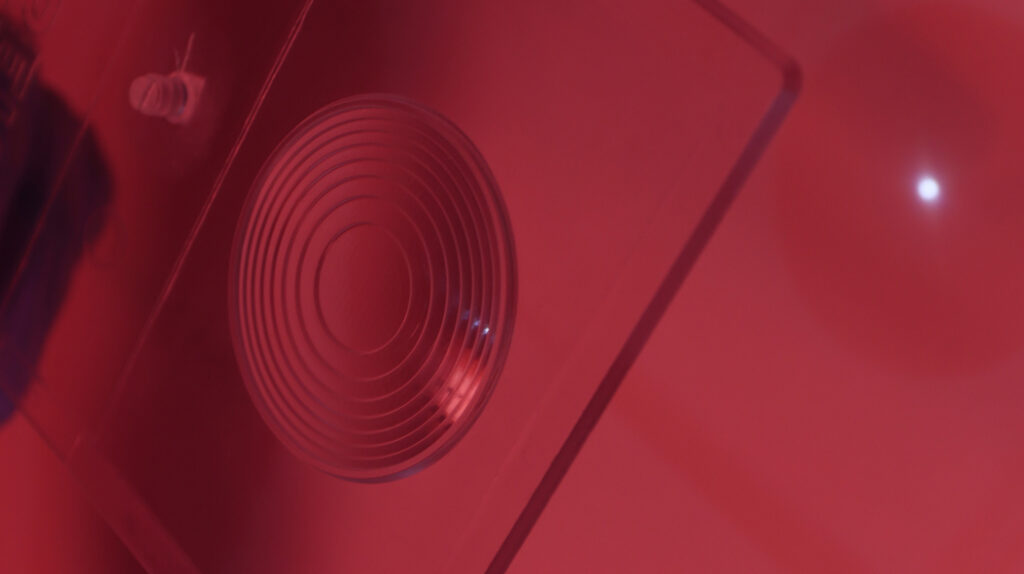
Injection molding microfluidics process definition
In applications involving low stress, thin walls, and microstructure replication, achieving the desired results heavily relies on precisely setting the […]