Microfluidic chips and their manufacturing processes
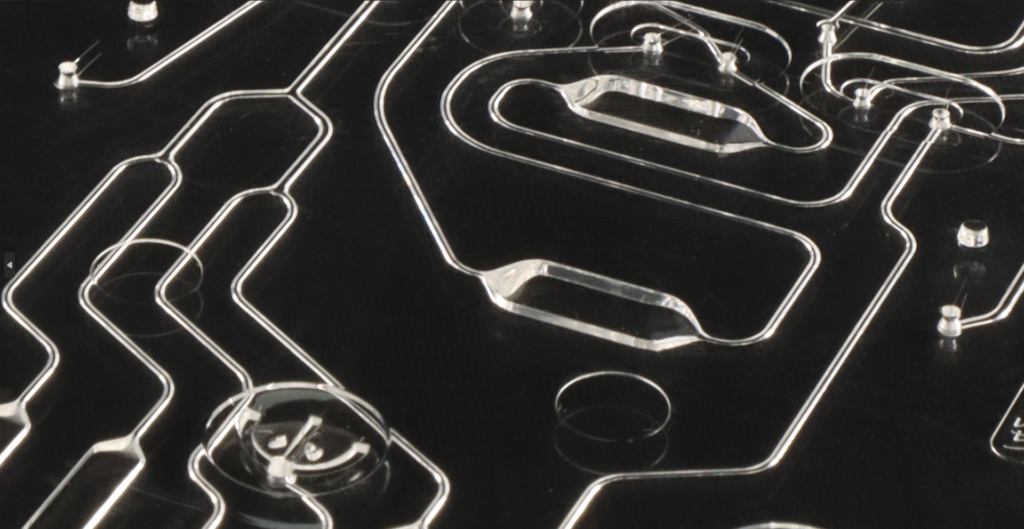
What is a microfluidic chip?
Many studies and new products are being developed in last years regarding microfluidic chips applications. The idea of using very small amount of sample quantity, a big reduction in reagents utilization, and a time reduction in testing results are the key ideas that are guiding these applications. Point of Care diagnostic applications, cell culture applications, lab on chip products for investigation or organ on a chip products for pharma testing are some of the fields where these Microfluidic devices are used.
Most of these applications will need an electronic hardware to control and monitor the test done, with elements such as: pumps for liquids moving, reagents dosing systems, result reading elements, HMI for configuration and operation… but also will need an only one usage cartridge where the reaction will be carried out, with some sample and needed reactives. This is what we will call the microfluidic chip.
How are microfluidic chips made?
The manufacturing of these chips can be done using different technologies, that could be selected due to the test characteristics, quantity of parts to be manufactured or the type of microfluidic structures needed to get the results. These could go from direct machining of polymer plates, though PDMS embossing, 3D printing or injection molding process. Due to the characteristic of quick and cheap mass fabrication process, the injection molding one will be the best option for medium to high volume parts manufacturing in terms of cost-quality ratios.
The mold in the injection molding process is the core, and to have the molds manufacturing completely under control is another key point. Moreover, to have a facility with the complete mold manufacturing in house with microlling capabilities to get proper channels definition in few microns, gives you a total control of your mold and a quick reaction time for reparation and modification of the tools.
Polymers for microfluidics
Regarding the materials used on these kind of chips, polymer materials are the most used for large scale production, the characteristics of medical grade polymer materials as cyclic olefin copolymer (COC), COP, polymethylmethacrylate (PMMA), polycarbonate (PC), Polystyrene (PS)… gives the desired optical characteristics, biocompatibility and great range of glass transition temperatures, that will help to temperature based analysis or to determined sterilization processes.
The usage of polymers and its behaviour due to contraction or shrinkage when it cools down is something that has to be taken into account always while designing these kind of chips, an appropriate design taking into account these properties is a must to avoid deformation problems in the parts, so it will be important to make a manufacturing redesign of the component with the appropriate injection points, thickness across the part, venting, injection type etc… Simulation software to analyse component injection and cooling phase will guide the decision to make on the design for manufacturing.
ERREKA: Your Trusted Partner for Polymer Microfluidic Chip Fabrication
Above that Erreka developed the knowledge to be a solid partner for the polymer components need in the microfluidic chip fabrication. Several components have been injected in our ISO 8 clean room using different injection process types such as Standard injection molding, Injection –compresion molding, or Heat&Cool injection process and always following the ISO13485 standard.
Contact us if you have any need for polymer microfluidic chips.
News
We tell you the latest news about ERREKA.
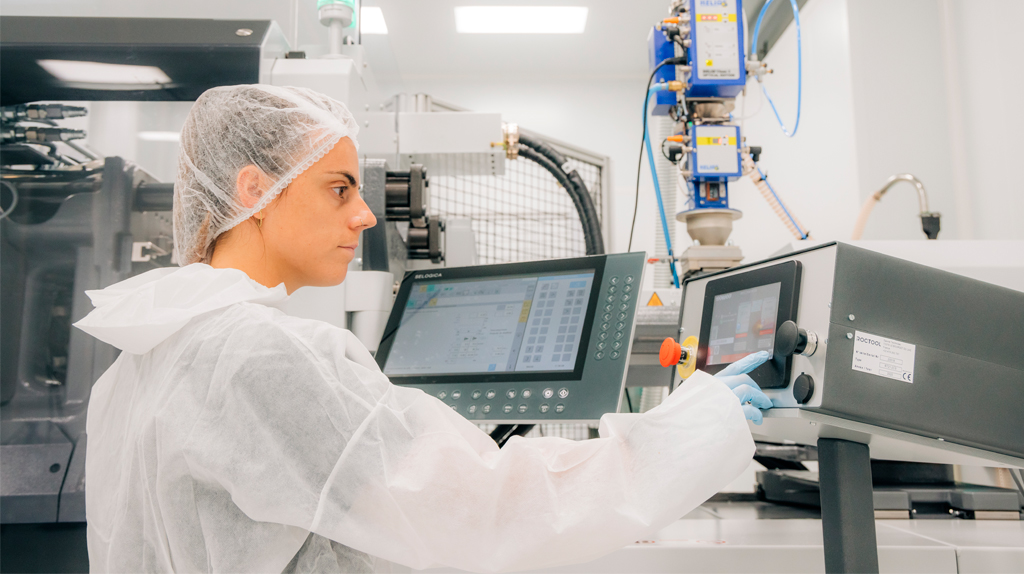
Polymer Science: Driving Innovation in Health and Industry
Polymer science enables the production of devices for a wide range of applications, including biomedical diagnostic (such as point-of-care diagnostics, […]
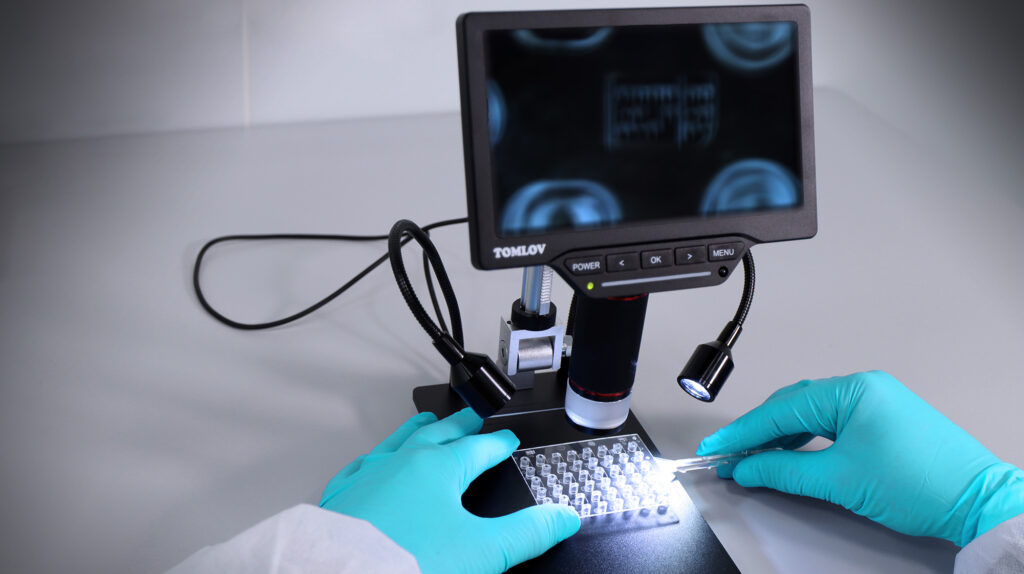
IVD Raw materials
With the enhancement of medical science and technology, there’s a growing need for real-time diagnostic devices. Many compact systems have […]
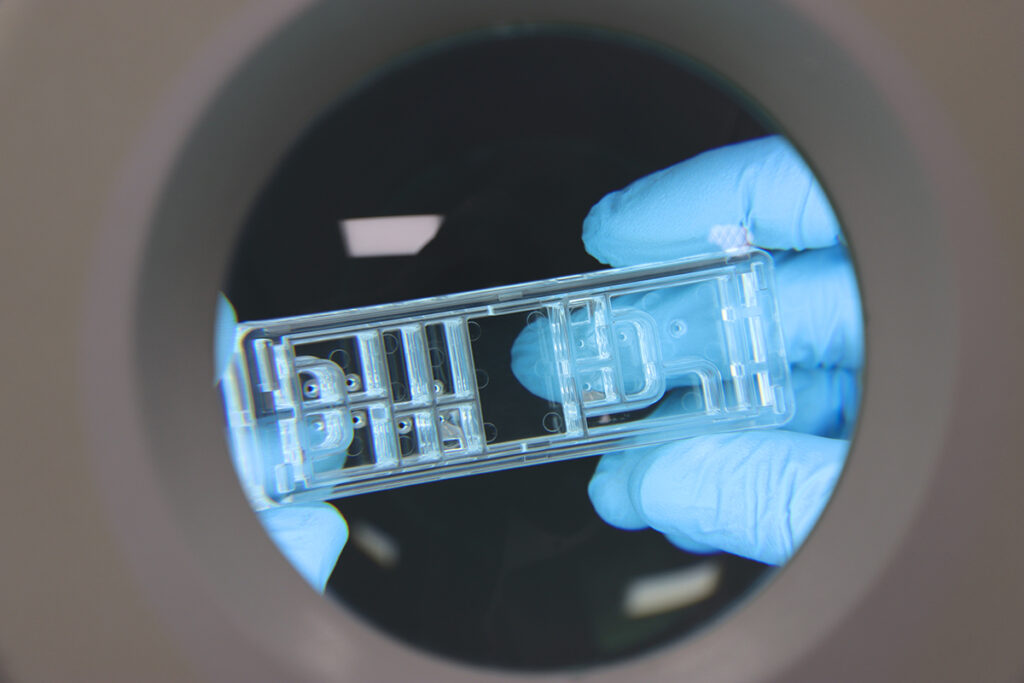
From glass chips to polymer chips: revolutionizing microfluidic technology
For many years, glass chips have been integral to biomedical applications, notably in microfluidic technology. However, recent advancements have illuminated […]